It’s surprising how many architects and designers are out there still using 2D design tools to draw their projects. We work in 3D and could never look back at designing a whole building or house in 2D, especially when it comes to the steel and timberwork.
Here at Arcline we start every project on paper, with a pencil. This is to get ideas down without the constraints of a computer program. But as soon as we have the overall design size and direction sorted, we model the building up in 3D on our design programs, starting with the basic shape and then getting into more detail with timber and steel, connections and heights/lengths.
It’s very obvious that in NZ we use alot of timber. Steel however, provides a solution when the timber size and use gets too sizey for certain spans, which is where we switch to using engineered steel.
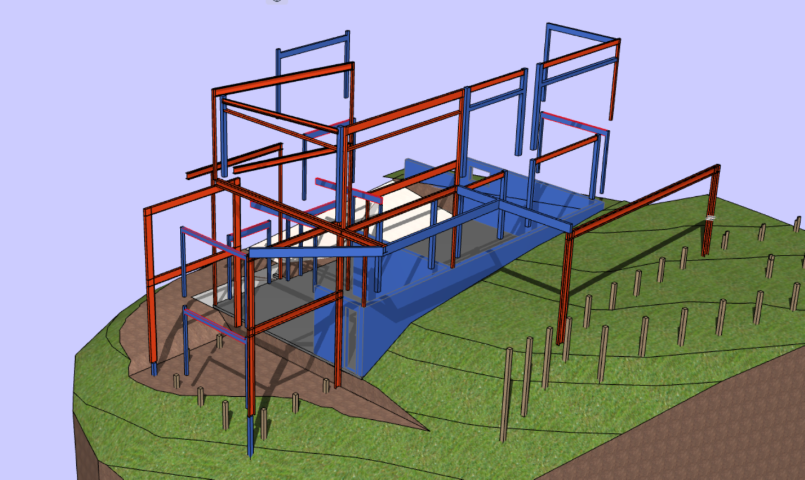
The Challenge With Steel
Ask any builder, and they’ll have been on a job where the steel beams, portals or lintels arrive onsite and they are slightly the wrong size. What we mean by slightly is – 1mm, or 4mm, or 12mm. Steel is very specific and cannot be bent, moved or forced into any tight areas. This is the big difference with timber where you can nip a few millimeters off the end of the joist or rafter to make it fit. Not so easy with steel, you have to cut it (accurately, not with an angle grinder!) and then have a certified welder weld it back together again to the correct length.
Engineers Decide The Size & Fixings
On most projects it is up to the structural engineer to decide the size of each steel member. He/she takes into account the Geotechnical report, which determines the foundation design, then considers the span and weight that the steel member is taking before calculating the size and style of steel member that will be used in said location.
Designers Include in the Plans
We (the designers) then ensure that the steel members selected will suit the plans and not hinder the look or style of the house or building. In our case, this is where we 3D model the steel into the home to ensure there’s no clashes with other timber or steel members, and that heights, connections and fixings can be accurately determined prior to construction starting.
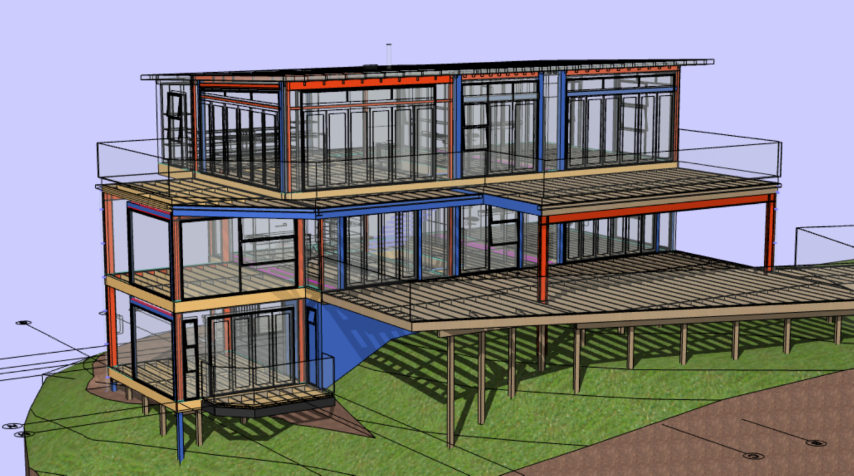
Building The Home Virtually
Our job as designers is to decide on the look, style, shape and layout of the home, and then work out to virtually ‘build’ the home so that when it comes to the builder onsite, everything has been thought of and worked out to save them time and confusion.
Saving Time & Money
We often get asked how we can justify being more expensive than other prices a potential client has received. As you can see above, you need to be sure you’re comparing apples with apples. With our method, we’re saving costly issues and mistakes that happen onsite. When a build project is underway it’s not unusual to get a call from your builder saying ‘hey we’ve hit x problem, which will cost 15 grand to solve, no one worked it out earlier that it was going to happen’.
By using Arcline, you’ll save money in the long run.
